Toyota - Camry - Workshop Manual - 2002 - 2006
Get your hands on the complete Toyota factory workshop software
Download nowGet your hands on the Complete Toyota Factory Workshop Software
Download nowGet notified when we add a new ToyotaCamry Manual
We cover 60 Toyota vehicles, were you looking for one of these?
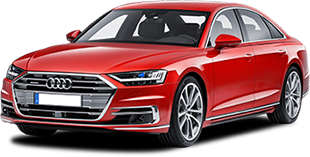
Toyota Sequoia 2001-2007 Service Repair Manual PDF
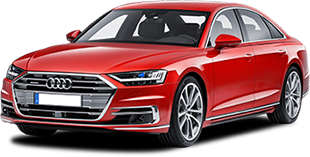
Toyota Prius 2003-2006 Service and Repair Manual
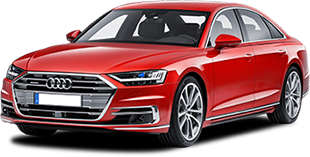
2010 Toyota Corolla Repair Manual (RM0000010EW133X)
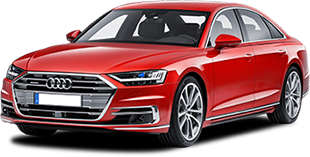
1994 Toyota Celica Service Repair Manual PDF
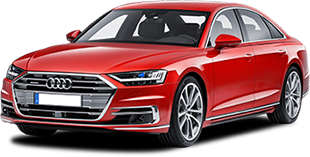
Toyota - Corolla - Wiring Diagram - 2001 - 2004
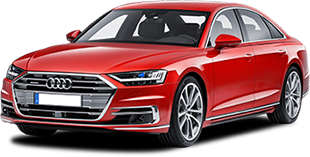
Toyota Prius 2004 NHW20 Service and Repair Manual PDF
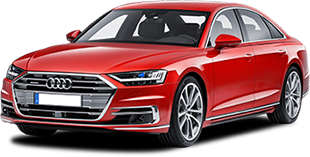
Toyota - Echo - Workshop Manual - 2000 - 2008
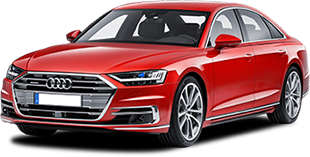
Toyota Hiace Electrical Wiring Diagram
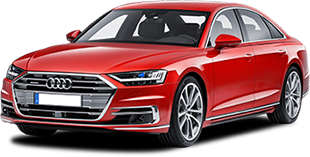
Toyota Avalon 2001 Service Repair Manual (RM808U) PDF
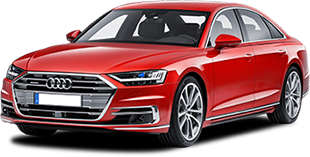
Toyota - Fortuner - Owners Manual - 2017 - 2017
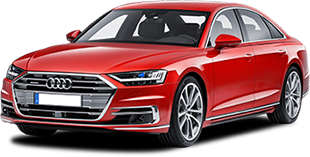
2007 Toyota FJCruiser Service Repair Manual PDF
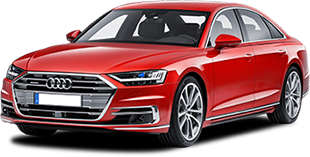
2005 Toyota Highlander Repair Manual (RM1144U)
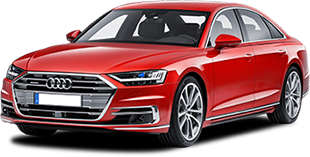
2001 Toyota Sienna Service and Repair Manual (RM787U)
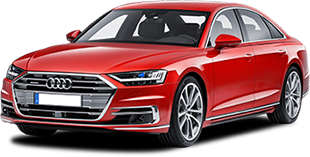
Toyota - Corolla - Workshop Manual - 2004 - 2004 (2)
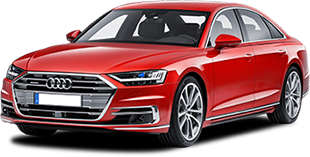
Toyota Avensis 1998-2002 Service Repair Manual PDF
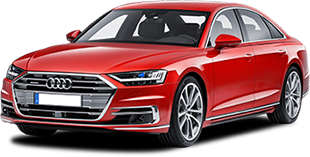
2005 Toyota Sienna (MCL20, MCL23, MCL25 Series) Repair Manual (RM1163U)
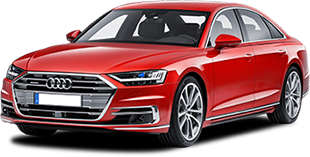
1999-2000 Toyota Celica Service Repair Manual PDF
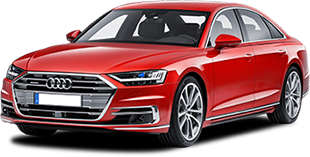
Toyota - Sequoia - Workshop Manual - 2001 - 2004
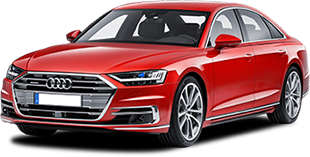
Toyota Corolla 2006 Electrical Wiring Diagram (EM00H0U)
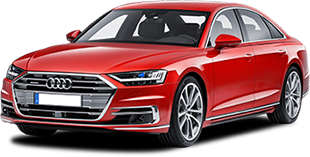
Toyota - Avalon - Workshop Manual - 2004 - 2006
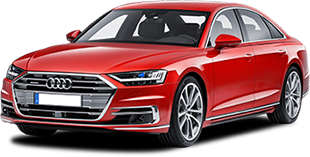
Tundra 2WD V8-5.7L (3UR-FE) (2007)
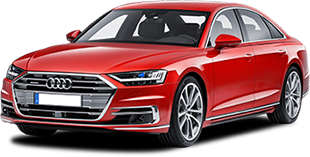
1995-1997 Toyota Tacoma Service Repair Manual PDF
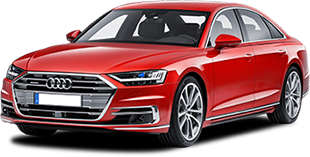
Toyota - Corolla - Wiring Diagram - 2000 - 2002
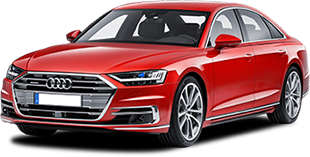
2001 Toyota Prius NHW11 Electrical Wiring Diagram PDF
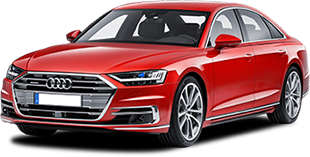
2001 Toyota Yaris, Echo Repair Manual For Chassis & Body (RM910E)
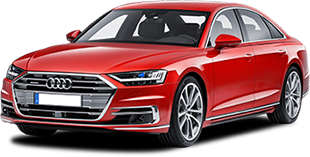
2007 Toyota Prius Electrical Wiring Diagram PDF
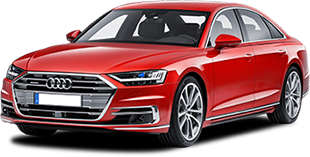
Toyota - Solara - Workshop Manual - 2004 - 2004
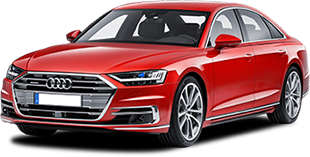
Toyota - Tacoma - Wiring Diagram - 2006 - 2006
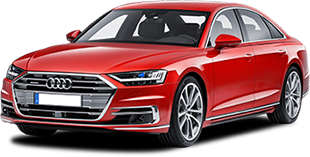
Toyota - Estima - Owners Manual - 2002 - 2003
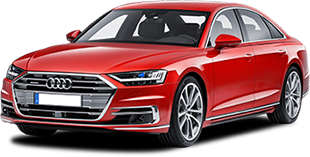
Toyota - Fortuner - Workshop Manual - 2012 - 2012
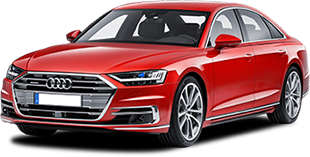
Toyota - Land Cruiser - Repair Guide - (1999)
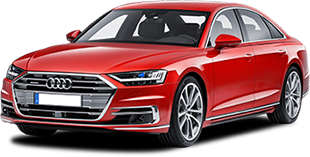
Tundra Access Cab LTD 4WD V8-4.7L (2UZ-FE) (2001)
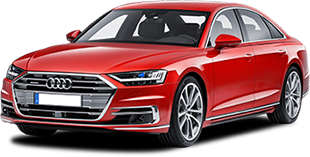
Toyota Prius 2003 Repair Manual
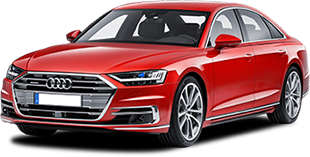
Toyota - Sequoia - Wiring Diagram - 2007 - 2008
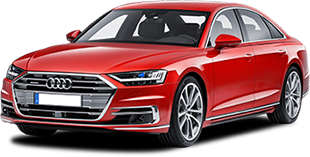
2002-2007 Toyota Avensis Chassis Wiring Diagram Engine Body Repair Manual
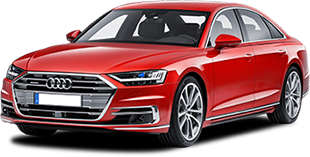
Toyota - Avensis - Workshop Manual - 1997 - 2018
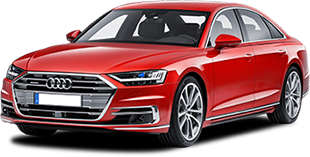
Tercel Sedan 2-Door L4-1497cc 1.5L DOHC (5E-FE) MFI (1997)
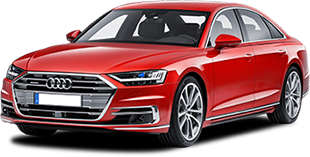
Toyota - Hilux - Owners Manual - 2015 - 2015
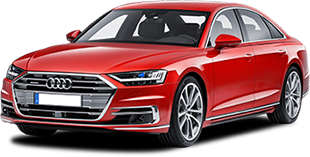
Toyota - Ractis - Workshop Manual - 2008 - 2008
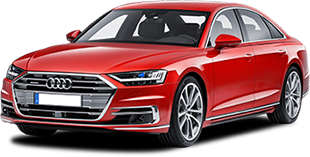
Toyota - Corolla - Workshop Manual - 2009 - 2020
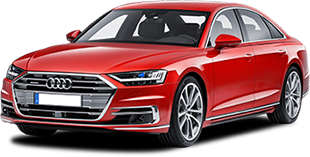
Toyota - Prius - Workshop Manual - 2009 - 2013
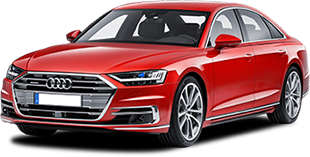
Toyota - Verso - Workshop Manual - 2004 - 2007
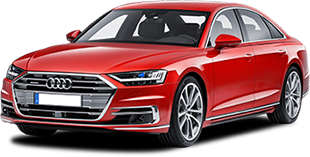
1988-1997--Toyota--Corolla--4 Cylinders A 1.6L MFI DOHC--31054901
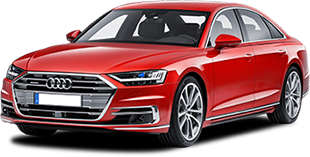
Toyota - Fortuner - Owners Manual - 2016 - 2016
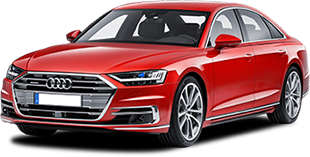
Tacoma Regular Cab 2WD L4-2.4L (2RZ-FE) (2000)
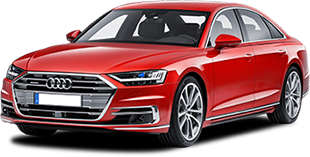
1983-1990--Toyota--Cressida--6 Cylinders M 3.0L MFI DOHC--31055001
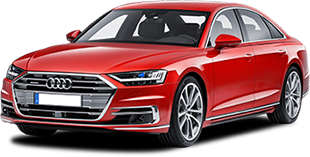
Tacoma PreRunner Dbl Cab 2WD V6-3.4L (5VZ-FE) (2001)
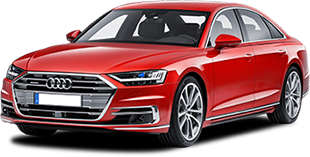
Tacoma Extra Cab 4WD V6-3.4L (5VZ-FE) (1998)
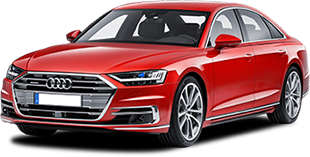
Venza AWD V6-3.5L (2GR-FE) (2010)
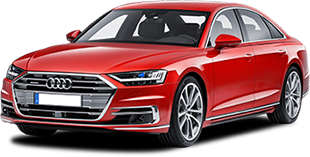
Toyota - Previa - Workshop Manual - 2003 - 2003
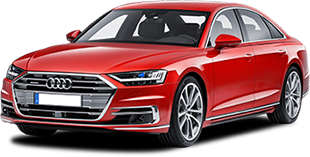
Toyota - Tacoma - Workshop Manual - 2003 - 2018
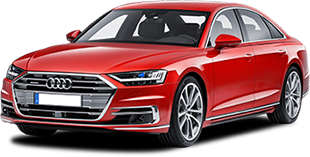
Toyota - Wish - Sales Brochure - 2008 - 2008
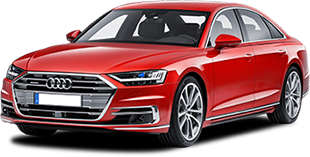
Tundra 4WD V8-4.7L (2UZ-FE) (2003)
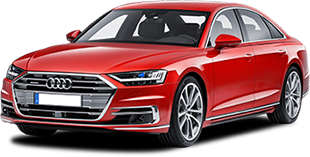
1999-05--Toyota--Corolla--4 Cylinders R 1.8L MFI DOHC--32606801
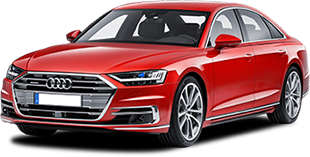
Toyota - Tercel - Workshop Manual - 1996 - 1996
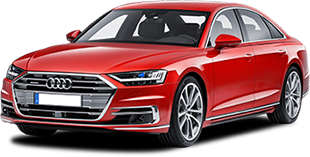
Toyota Hiace Body Repair Manual for Collision Damage
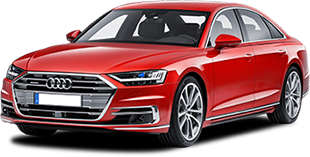
Toyota - Ipsum - Workshop Manual - 1995 - 2009.PDF
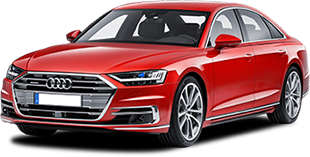
Toyota - Auto - 2008-yaris-hatchback-manual
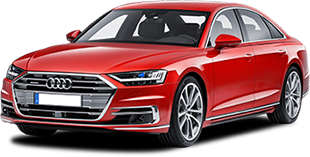
Toyota - Fortuner - Workshop Manual - 2015 - 2015
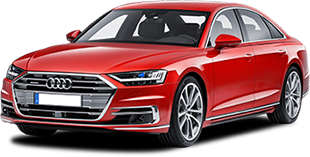
Tundra Access Cab LTD 2WD V8-4.7L (2UZ-FE) (2000)
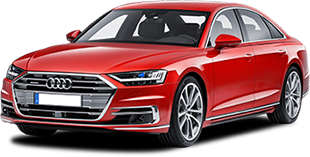
Toyota Sequoia 2001-2007 Service Repair Manual PDF
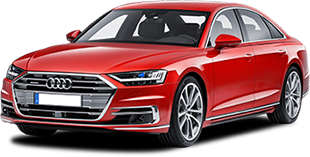
Toyota Prius 2003-2006 Service and Repair Manual
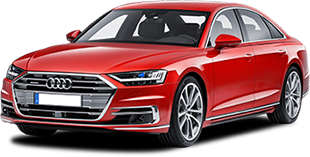
2010 Toyota Corolla Repair Manual (RM0000010EW133X)
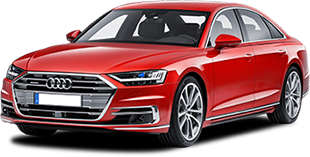
1994 Toyota Celica Service Repair Manual PDF
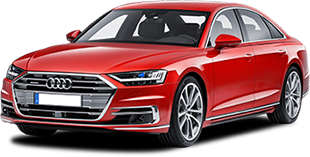
Toyota - Corolla - Wiring Diagram - 2001 - 2004
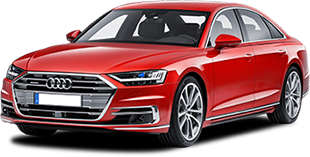
Toyota Prius 2004 NHW20 Service and Repair Manual PDF
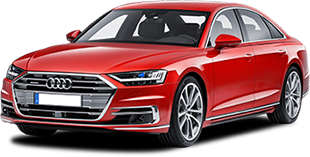
Toyota - Echo - Workshop Manual - 2000 - 2008
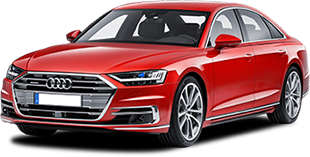
Toyota Hiace Electrical Wiring Diagram
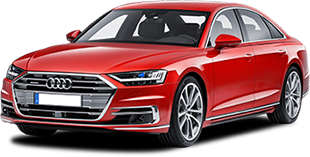
Toyota Avalon 2001 Service Repair Manual (RM808U) PDF
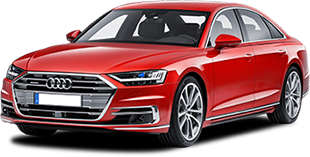